When you think of a typical Sydney warehouse, you probably picture towering shelves packed with stock, forklifts zipping between loading bays, and constant activity around the clock. But there’s one crucial part of every warehouse that often goes unnoticed — until it fails: the floor.
Warehouse floors in Sydney have to withstand an extraordinary amount of punishment. Between heavy machinery, high traffic, pallet jacks, oil spills, and Australia’s often humid coastal climate, an ordinary concrete floor just isn’t up to the task. That’s where warehouse epoxy flooring comes in — and in 2025, it’s one of the smartest investments Sydney warehouse owners can make.
In this comprehensive guide, we’ll take you through everything you need to know about industrial epoxy flooring in Sydney — from the benefits and types of systems available to costs, maintenance, and how to choose the right installer for your business.
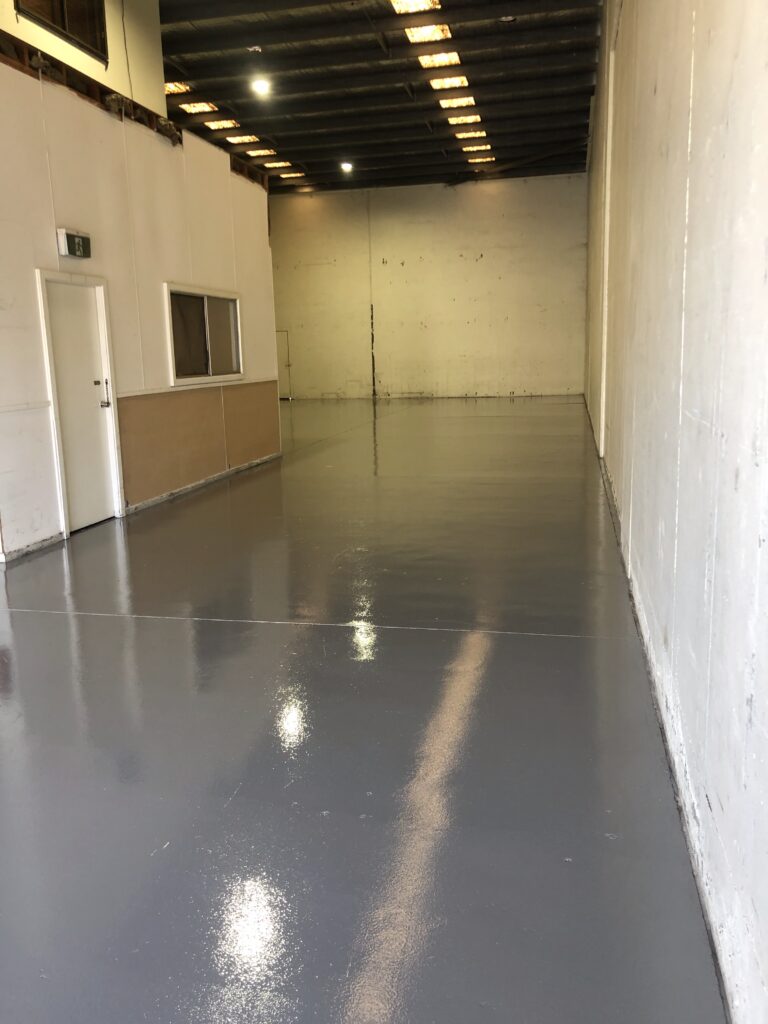
Why Warehouse Floors in Sydney Need Something Special
If you run or manage a warehouse in Sydney, you already know it’s a tough environment:
- Forklifts and pallet jacks can wear down unprotected concrete fast
- Chemical spills can permanently stain or damage the floor
- Dust from bare concrete can contaminate products — especially in food and pharma storage
- Uneven or cracked floors are an OH&S hazard waiting to happen
- Sydney’s coastal air brings moisture → this accelerates concrete degradation
In short, a standard untreated concrete floor won’t last long under these conditions. And frequent floor repairs are both expensive and disruptive.
That’s why many Sydney warehouse operators now turn to epoxy flooring systems — purpose-built to handle these challenges and keep warehouses running smoothly.
What Is Epoxy Flooring?
Put simply, epoxy flooring is a multi-layer system where a two-part resin (epoxy + hardener) chemically reacts to form a tough, plastic-like surface that bonds to the concrete below.
Unlike paint, epoxy becomes a fully hardened surface:
✅ Resistant to chemicals, oils, and water
✅ Withstands physical impacts and abrasion
✅ Seals and strengthens the concrete underneath
✅ Available in smooth or textured finishes
✅ Seamless → no grout lines or cracks to trap dirt
In a warehouse setting, this means you get a floor that:
- Won’t chip or flake under forklift wheels
- Won’t absorb oil or chemical spills
- Is easy to clean and maintain
- Improves safety through non-slip finishes
- Looks professional → important for client-facing spaces
Benefits of Epoxy Flooring for Sydney Warehouses
Let’s look at the key advantages in more detail:
1️⃣ Extreme Durability
Epoxy flooring is built to take abuse:
- Forklifts? No problem.
- Heavy storage racks? Handled.
- Constant foot traffic? Shrugs it off.
Where bare concrete would wear down, an epoxy floor maintains its integrity year after year.
2️⃣ Chemical Resistance
Many Sydney warehouses handle:
- Oils and lubricants
- Cleaning agents
- Acids and solvents
- Food and beverage spills
A high-grade epoxy system is formulated to resist chemical damage — protecting both the floor and any goods stored in the space.
3️⃣ Hygiene and Cleanability
Bare concrete is porous → dust and bacteria can settle in.
Epoxy creates a seamless, non-porous surface:
✅ No dusting
✅ No trapped dirt
✅ Easy to mop or scrub
This is critical for:
- Food storage warehouses
- Pharma and health products
- Electronics
- Anything sensitive to contamination
4️⃣ Safety Improvement
Warehouse floors can be dangerous when:
- Wet from spills
- Covered in fine dust
- Uneven or cracked
An epoxy floor allows you to:
✅ Add slip-resistant textures
✅ Clearly mark pedestrian walkways
✅ Colour-code work zones for safety
Many Sydney warehouses have improved their OH&S compliance through epoxy upgrades.
5️⃣ Cost-Effectiveness
While installing epoxy flooring is an upfront investment, it pays off fast:
- Less floor maintenance
- Reduced need for repairs
- Fewer disruptions to warehouse operations
- Improved safety = lower liability risks
In the long run, a quality epoxy system is cheaper than repeatedly fixing damaged concrete.
Types of Warehouse Epoxy Flooring Systems
Epoxy isn’t one-size-fits-all. Different systems suit different needs.
Here are the main types used in Sydney warehouses:
Self-Levelling Epoxy
✅ High-gloss, seamless finish
✅ Ideal for high forklift traffic areas
✅ Provides a perfectly smooth surface for efficient operations
✅ Easy to clean → great for hygiene-focused warehouses
Quartz-Filled Epoxy
✅ Epoxy combined with quartz sand aggregate
✅ Creates a highly textured, anti-slip surface
✅ Perfect for wet areas or where extra grip is needed → beverage warehouses, freezer storage
✅ Very durable → withstands heavy mechanical impacts
Flake Epoxy
✅ Decorative finish → often used in customer-facing warehouse zones
✅ Coloured vinyl flakes broadcast into the epoxy
✅ Provides both durability and aesthetics
✅ Not as industrial as self-levelling or quartz → use where appearance matters
Novolac Epoxy
✅ Extreme chemical resistance
✅ Used in specialist warehouses handling aggressive chemicals
✅ Often combined with other coatings for maximum protection
Anti-Static Epoxy
✅ Prevents static build-up → critical for:
- Electronics storage
- Data centres
- Explosives / flammables storage
✅ Special anti-static agents incorporated in the epoxy system
Installation Process — What to Expect
Here’s a typical flow for installing epoxy in a Sydney warehouse:
1️⃣ Assessment & Prep
- Floor condition evaluated → repairs as needed
- Surface preparation → diamond grinding / shot blasting → critical for adhesion
- Any contamination removed
2️⃣ Priming
- Primer coat applied to promote strong chemical bond to concrete
3️⃣ Base & Broadcast
- Base epoxy layers applied → thickness tailored to traffic/load
- Broadcast aggregate (quartz, flakes) if needed → for slip resistance
4️⃣ Topcoat
- UV-stable topcoat for added durability and chemical resistance
- Finishes range from matte to gloss depending on operational needs
👉 Installation time:
3–5 days typical for medium-sized warehouse (1000–2000 m²)
👉 Cure time:
✅ Light foot traffic: ~24 hrs
✅ Full mechanical traffic (forklifts): 5–7 days
Cost of Warehouse Epoxy Flooring in Sydney (2025)
Here’s a ballpark guide for budgeting:
System Type | Cost Range (per m²) |
Self-Levelling | $70–$120 |
Quartz-Filled | $90–$140 |
Flake | $80–$130 |
Novolac / Anti-Static | $120–$200 |
👉 Factors affecting cost:
- Floor size → larger jobs get economies of scale
- Condition of concrete → poor slabs require more prep → adds cost
- System type → chemical-resistant and anti-static systems cost more
- Site access → upper level, tight sites add to project complexity
Maintenance Tips
An epoxy floor needs simple, consistent care:
✅ Daily sweep to remove grit
✅ Weekly scrub with neutral pH cleaner
✅ Clean chemical spills promptly
✅ Periodic inspection for topcoat wear (re-coat as needed after years of heavy use)
With basic maintenance, a quality warehouse epoxy floor lasts 10–15 years, sometimes even longer.
Choosing an Epoxy Contractor in Sydney
👉 Not all epoxy installers are created equal. Look for:
✅ Proven experience with warehouse-scale projects
✅ Correct surface prep → critical for durability
✅ Use of industrial-grade resins → not DIY garage kits
✅ Willingness to tailor system to your operational needs
✅ Solid references and case studies in Sydney
✅ Clear warranty terms
Final Thoughts
Sydney warehouses face demanding environments — and your flooring needs to match that. Epoxy flooring provides:
✅ Durability
✅ Chemical resistance
✅ Hygiene
✅ Safety
✅ Long-term cost savings
If you want to upgrade your warehouse floors to a system that works as hard as your team, consider epoxy — it’s a proven performer in Sydney’s most demanding industries.
👉 To explore your options for epoxy flooring in Sydney, speak with our specialists today.